What are single acting & double acting hydraulic cylinders?
A hydraulic cylinder works on the principle of pressure difference. The hydraulic cylinders can be broadly categorised into:
- Single acting cylinders –Where the pressure can be applied only in one direction and the return of the piston is either by gravity or other means such as pulling back (A bicycle air pressure filling pump).
- Double acting cylinders – in these cylinders the pressure can be applied from both the sides. The other side acts as the return side (low pressure) in the forward stroke and acts as the main side (high pressure) in the return stroke. This cylinder has openings on both sides to allow for hydraulic oil to enter and exit (return to tank) from both sides alternately as per the stroke (forward or return).
The hydraulic basically acts on the simple principle of Force and pressure.
Force (F) = Pressure (P)*Area (A)
The force exerted on the cylinder piston rod of the cylinder is equal to the pressure of the hydraulic oil multiplied by the area of the piston. The force exerted on the piston in the forward (main) stroke is higher than the force on the other side of the piston since the pressure on the other side is very low (equal to the tank or reservoir pressure). This difference in force results into the movement of the piston towards one end of the cylinder tube and the subsequent movement of cylinder rod out of the cylinder or inside the cylinder as the case may be (double acting). The piston rod is attached to the piston and may be considered integral with the piston since they both move together only.
The main parts of a double acting hydraulic cylinder are:
- Cylinder tube
- Piston
- Piston Rod
- Head End Cover (Cylinder Head)
- Piston Seal (Part of cylinder seal kit which also contains the dust seal fitted in head end cover)
- Attached pipes (to entry and exit ports on the cylinder tube)
Further, once the piston moves to one end of the cylinder tube and still the hydraulic oil pressure is applied then the pressure gets relieved through a pressure relief valve located in the hydraulic system which is set to a predetermined pressure value. Moreover, if there is an internal leak (the seal may be cut inside and allow the oil to leak to the other side of the piston although no leakage may be visible from the outside) in the piston seal then the pressure gets relieved from there before the relief valve setting is reached and in such a case, the cylinder does not create the force which it normally creates. It basically underperforms. If this happens, then the piston seal kit needs to be replaced.
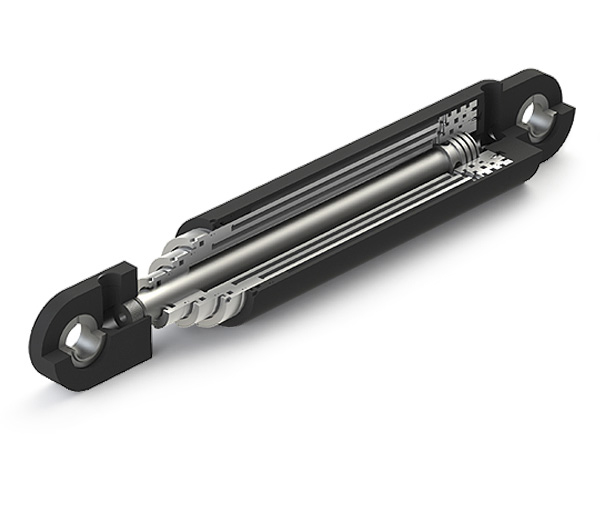